CNC machining is a manufacturing process that utilizes computerized controls to operate and manipulate machine and cutting tools to shape stock material—e.g., metal, plastic, wood, foam, composite, etc.—into custom parts and designs.
An axis reference is used to describe a CNC machine that works with multiple axis points. The machine operates in the XYZ plane with at least three axes: X-axis (vertical), Y-axis (horizontal), and Z-axis (depth). The 4th axis is with the A axis (rotation around the X-axis), and the 5th axis includes the B-axis (rotation around the Y-axis).
So what are the differences between 3 axes, 4 axes, and 5 axis CNC machining, the following provides an explanation of it.

3 Axis CNC machining
3-Axis machining is the most simple type of machining, where the workpiece position is fixed, while the cutting tool moves along the X, Y, and Z linear directions to cut away material. This is good for the parts that don’t need a lot of depth and detail. Only one side of the part can be machined for a single fixture setup. 3 axis machining is used to produce mechanical components normally and is suitable for:
- Automatic/interactive operation
- Milling slots
- Drilling holes
- Cutting sharp edges
4 Axis machining
4-axis machining means that a workpiece is processed in an equal manner as a 3-axis system, however, has an extra rotary movement around the X-axis, which is called the A axis. This rotation permits the workpiece to be cut around the A. When holes or cuts need to be made on the sides of a workpiece, this machining method is useful. This additional 4th axis (A axis) allows a workpiece to be mechanically flipped over, so the machine can cut away material from both sides. 4-axis machining is multifunctional and can be used for:
- Intermittent cutting
- Continuous cutting
- Engraving curved surfaces
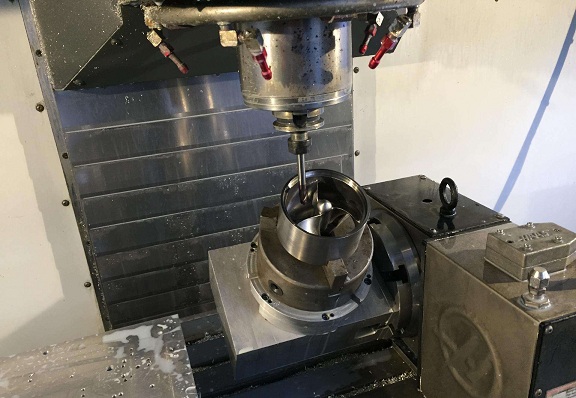
5 Axis CNC machining
5-axis machining means that a workpiece can be processed from five sides at one time. In addition to movements along the X, Y, and Z-axis, the machine utilize 2 out of the 3 possible rotation axis(A, B, C), the A, B, and C axis perform a 180° rotation around the X, Y, and Z-axis Normally, the A-axis and B axis will be used as rotational axis on the 5-axis CNC machining. 5-axis machining is one of the multiaxis machining.
There are two types of 5-axis CNC machines normally, 3+2 machines, and fully continuous 5-axis machines.
In 3+2 axis machining, the two rotational axes perform independently to each other, which means that the workpiece can be rotated to any compound angle with respect to the cutting tool. However, it is impossible to rotate both axes at the same time. 3+2 machining can manufacture especially complicated 3D geometries.
Fully continuous 5-axis machining allows simultaneous rotation of two rotary axes, at the same time as machining and the cutting tool moving linearly in XYZ coordinates. The continuous 5-axis machining can produce very complex 3D geometry, not only planar compound angled features but also complicated curved 3D surfaces, giving us the capability to produce parts normally reserved for molding processes.
This type of machining is used in the automobile, aerospace, and boating industries. 5 axis machining is beneficial when components are very complex and with high precision. This includes:
- Accuracy Features
- Increased productivity
- Higher quality finishes
- Cutting intricate details
- Machining complex geometry